 |

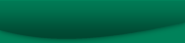 |
|
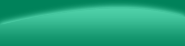
 |
© 1999-2004
Association of Lifecasters International
All rights reserved. |
|
 |
 |
|

FORUMS
|
|
|
 |
Author |
Message |
Ed McCormick
Joined:
: 21-Mar-2004
|
Started On : 15-Oct-2005 at 11:07:26 AM, #Views : 9277
Topic Subject : TECHNICAL BULLETIN - ALIGINATE |
|
Controlling the Quality of Your Alginate Impressions
All molding materials rely on two components to trigger its gel reaction – commonly referred to as Part A and Part B. The producer controls the quality of Part A. You must control the quality of Part B.
As formulators for a variety of alginate compounds since 1989, ArtMolds has received its share of technical questions from customers asking about the resolution of unexpected results. Before I describe them let me explain the basics of traditional alginate formulas. All molding materials rely on two components to trigger the chemical reaction (gelling or solidifying) – commonly referred to as Part A and Part B. Alginate impression materials are no different. They gel by combining a formulated mix of powdered chemicals (Part A) with a single liquid chemical - water (Part B).
The Part A
The powder formulas (Part A) are generally composed of from six to eight ingredients; alginate salts, a binder of metal salt, such as zinc sulfate or calcium sulfate, metal oxide for strength, a retarder based on phosphate, a filler of clay and perhaps a colorant along with a scent. Manufacturers have their own proprietary formulas for the percentage of each component part. It will vary from manufacturer to manufacturer. Thus you will have different results.
But what is the same are the chemicals used to create Part A are purchased in pure unadulterated form from the refiner. This means that if the overall alginate formula (Part A) contains 5-percent magnesium oxide (MgO), this chemical is pure and uncontaminated form of magnesium oxide. Through quality testing, the manufacturer can assure the purity and then control the precise amount of each ingredient in its formula.
The goal of the producer is to create a formula that does not vary from batch to batch. By testing, weighing ingredients and screening partial size this can be accomplished with precision.
Controlling Part B is up to you.
The Part B
All R&D laboratories use de-ionized or distilled water (pure H2O without the metal ions found in tap water) when a formulation calls for H2O. The same is true in quality control testing in chemical manufacturers. That is, their Part B is pure. However, except for dentists who are trained to know the importance of using pure ingredients, most alginate users ignore the fact that alginate formulations rely on a fairly precise combination of chemicals to create a repeatable predicted reaction.
For alginate formulations the producer is vulnerable as it can control only the purity of Part A. Its predications for the outcome of combining its powder with water must be based on a standard. It is. The water it uses is a soft generally mineral free liquid. It is up to user to test the degree with which its own water may diverge from the standard, as the manufacture can not.
I pointed out that Part A may contain calcium, zinc, magnesium and phosphate. Tap water and well water will also contain some if not all of these ingredients. Most of these are trace elements. So generally this is not a problem. Tap water can be used as most alginate formulas can forgive limited contamination. But in various regions there is sufficient quantity of these materials dissolved in the water to adversely affect the results of the impression material when mixed with tap water.
Excess phosphates will delay or prevent setting. The presence of added metal ions in water will cause a grainy mix and uneven gel formulation and can have an adverse effect on the control of set time. This problem is most serve in regions where water supply has a high metal content. It is particularly vexing in those regions where mineral content of water can vary throughout the day.
Test Before Using On Your Application
Therefore, if you are using tap water make certain you test a small batch by mixing it with the powder in the recommended proportions before you actually use the material for its intended application. Check for graininess and set times. If the results are not satisfactory, make a similar test using distilled water. If there is an improvement -- you have a water problem and should use distilled water for your Part B.
Summary
All molding materials rely on two components to trigger its gel reaction – commonly referred to as Part A and Part B. Alginates’ Part B is water. The producer carefully controls the purity of the Part A side. As the user you must be aware of the consequences of a contaminated Part B drawn from the tap. If you understand its significance you can readily resolve setting and mixing problems by substituting with pure water. More importantly, you will have better quality alginate impressions every time.
|
|
|
|
|
|
|