 |

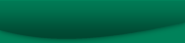 |
|
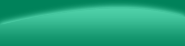
 |
© 1999-2004
Association of Lifecasters International
All rights reserved. |
|
 |
 |
|

FORUMS
|
|
|
 |
Author |
Message |
Dan Spector
Joined:
: 02-Jan-2008
|
Started On : 05-Aug-2009 at 06:32:45 AM, #Views : 8976
Topic Subject : Re: Re: Re: Re: New Lifecasters in UK |
|
Ali
Glad to help all who care to listen.
Because I have a plasterworking shop, I was ready to apply certain
techniques when I started lifecasting. At the start, I did pour a
couple of molds full of Hydrostone, the heaviest and strongest of the
USG plasters, and have some idea of the weight and the wait you speak
of. Then it struck me that the thickness was doing me no good, and i
might try using fiberglass mat as I do in my architectural work. The
weight of so much plaster also demands much stronger mothermold
walls. (In normal plaster factory work, thick plaster is poured into
latex molds which are inside stiff mothermolds, which are swirled
until it sets roughly equally-thick. This is good enough for lamps
but not for us.) Since Hydrostone cannot be slumped - does not
thicken in a slow progression, but takes a snap set - i stopped using
it, and went to the strong-enough Hydrocal. Pouring a bucket of this
into the mold, it is easy to slosh it all over the inside, and I use
pieces of mat as washcloths, which quickly fall apart; and I place
little bundles of wet fiberglass mat through the liquid into nipples
and fingers and toes, the places likely to snap off when I beat my
plaster molds apart.
So as the first batch takes a set, it had been roughly equally
sloshed into all parts of the mold and filled all the detail.
Immediately I follow with another batch but I place many small
squares of the mat into the bowl, and after spreading a thin layer of
H'cal, I quickly place the mat pieces all over the previous layer
slightly overlapping. If possible, I take time to rub them down into
the mold and so get a smooth surface. One more batch is added
perhaps with larger pieces of mat, and taking care to strengthen the
edge and all places the statue will need strength. Then I will bend
and cut a length of galvanized wire to serve as the hanger. A small
batch is mixed to wet the f'glass needed to embed the wire ends
shaped into hooks to resist yanking out of the matrix.
As soon as this last batch sets, I take a Surform with curved blade
or a mat knife and start going around the edge, pushing from inside
to out, to uncover the edge of the plaster mold (your mold will be
alginate/bandage i suppose.) Easier to do this now than after
Hydrocal reaches its full strength! Also, in the event I uncover a
too-thin wall, I will reinforce it at this time. But this does
produce life castings of remarkable strength and lightness, with an
average thickness of 1/3 - 1/2 inch. These dry completely in under a
week, depending on the weather. (I am awake at 4 am because we're
undergoing yet another thunderstorm.)
Now to complicate the process.. If I wished to give the cast a tint
I mixed color into at least the first two batches. I used to leave my
back sides rough, until I saw the work of Carol Feuerman in a NYC
gallery. She takes as much pains with the inside as the outer
surface! This wouldn't show on a piece hung flat against a wall but
it does matter on pedestal pieces. So I often tint my final layers a
darker shade and smooth the insides nicely.
Further: I was simplifying the truth saying I simply went to
Hydrocal. Back then, the USG rep wanted me to order Hydrocal FGR-95
so he special-ordered 5 sacks of it for me. This remarkable stuff
hardens slower than regular H'cal and is meant to be hand-rubbed.
This rubbing not only looks nice, it produces an effect called
felting, where the glass strands form a continuous membrane or layer
- very mighty. After that, I'd have to order an entire pallet of
FGR-95 which I never could do, but for those who can, I recommend it.
I will still start with plain Hydrocal for the surface, or add some
Hydrostone to it; then add FGR-95 50/50 to regular HCal to laminate
the inside.
By working fairly rapidly, the casting expands slowly and does not
have the cracking which one would expect if one cast a first layer
allowed it to thoroughly dry, and then laminated its inside.
Ali, you use terms such as stone and hession. I am supposing that
stone means plaster and hession - is this hemp? Hemp and sisal are
vegetable fibers used in plasterwork to great effect, but they don't
lend themselves to lying flat. I doubt they would felt well. If
weight were no object they'd do fine. But since weight means slower
drying and more trouble shipping and hanging, I don't favor them. If
I worked as thin as I possibly could, the cast would feel
insubstantial, even if very strong, so I don't try that hard! I
imagine that bandage or cheesecloth could be used instead; it will
lie flat.
I am always stressing the economy of my methods but let's face it
fiberglass mat as I use it comes in big rolls, and most could not
justify buying a roll. So if you like, I will ship mat in sheets or
already-cut squares to you; but a better idea is, find a local
fiberglass fabricator and buy some yards of the thinnest mat they
use. Mine comes 52" wide and is 3/4 ounce in thickness. I used to use
1 1/2 oz mat and literally ripped each square into thinner halves.
There, that's my full lesson. I hope it is useful to you.
Dan Spector
901 323 8717
www.lifecast-art.com
dan@archicast.com
On Aug 4, 2009, at 10:05 PM, aliforum@lifecasting.org wrote:
> ------------Silica-Free & Oh So GREEN------->
>
> NEW! MoldGel SILFREE. A revolutionary formula.
> Made with all food-grade ingredients. It nourishes
> the earth when discarded. 3-to-1 mix ratio yields
> twice the volume as those 1-to-1 brands. Delayed
> shrinkage for delayed casting - so creamy smooth, too.
> To learn more about it click here
> ---------------------------------------------->
>
>
> Hello Dan Spector
>
>
> Post Date : Tuesday 04th 2009f August 2009 10:58:51 PM
> Posted by : "Ali Webber" tawebber123@hotmail.com
>
> Re: Re: Re: New Lifecasters in UK:--
> Hi Dan
> Im reasonably new at this whole thing, so taking lots on board. I
> went and did some training to learn the basics. They showed me how
> to do casts of torsos, faces, baby hands and feet, 2d hands etc, i
> have recently done one of my best friends chest and then once i had
> the mould i reinforced the back and literally poured full of stone
> - extremley heavy, it has a stainless steel pole going thru the
> centre which i was going to mount onto a block of something thats
> strong!!!!!! I have not yet been taught how to do layering i was
> told that it is mostly used for pregnant bellies and that little
> bit of stone is poured followed by layering with bandages. I was
> told that i would have to be trained seperatley on this as its
> complicted but i will pretty much have a go at anything. I think
> they then said that whole process was repeated a couple of times
> but i think i like the sound of the fibreglass better. Do you mind
> running thru that with me, do you only do one layer or a couple
> like this and do you have to wait until it completley drys before
> you do the next layer? I was also advised at my training that even
> babys hands and feet should be left to cure for at least 4 weeks
> before sealing with gesso and painting. You obviously have a wealth
> of knowledge, and i may have been misinformed. This is the beauty
> of this industry everyone has different ideas. Thanks for your
> comments, Ali
>
> ALI is an international organization whose members are engaged in
> the art and creative industries. Its purpose is to promote the art
> of life casting, create public awareness of this unique art form
> provide its members with forums to exchange information, resources
> to enhance their effectiveness and advance opportunities for their
> artistic success.
|
|
|
|
|
|
|